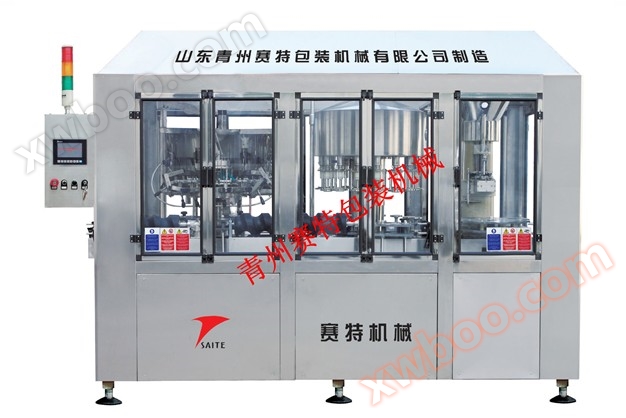
fillingThe valve adopts negative pressure liquid level filling developed by # #, which makes the filling speed faster and more stable. At the same time, various imported electrical components with relatively stable performance are used. The whole machine uses the same operating system for speed regulation, with good overall coordination. Multiple screw bottle conveying and bottle clamping mechanisms are installed at the inlet and outlet of the bottle, and a photoelectric control system is also equipped. In case of abnormal situations, the whole line will be shut down. Therefore, compared with machines of the same specifications, this machine has higher output, greater efficiency, simpler operation, and higher degree of automation. It is an ideal # # equipment for wine and fruit wine manufacturers.
The electronic control system uses PLC human-machine interface, color touch screen, imported photoelectric sensors, etc.
Wine filling machineEasy to operate, this machine uses the powerful information exchange platform of PLC to easily achieve information such as pipeline counting and timing, and automatic fault diagnosis to understand the cause of the fault and quickly and promptly repair it.
1. Characteristics of bottle washing machine
(1) Fully automated production has been achieved through the use of elastic and powerful robotic arms for bottle grasping, flipping, rinsing, bottle control, flipping and resetting, and bottle dispensing processes. (2) Continuous tracking bottle flushing has high efficiency and stable flushing effect. (3) Adopting international # # frequency converter for variable frequency speed regulation, the speed can be freely controlled. (4) The flip robotic arm developed by introducing foreign technology has the advantages of bottle grasping and positioning, flexible flipping movement, good sealing performance of the flushing valve, and high bottle flushing force with accurate alignment of the bottle mouth. (5) The bottle guide screw and dial processed by CNC engraving center are used for bottle entry and exit, and the bottles # # are guided into the bottle entry track, effectively solving the problems of bottle squeezing, bottle jamming, bottle blockage, and bottle breakage. (6) Simply press the lift button and replace the corresponding bottle diameter dial to change bottles of different diameters and heights, making adjustments convenient and effortless. 2. Characteristics of filling machine: (1) Wide range: Suitable for bottle diameters of 60-100mm, bottle heights of 250-350mm, with a large filling capacity range and easy adjustment. (2) Full compatibility: Various circular containers such as glass, porcelain, plastic, and ceramic bottles can achieve fully automated operations. This machine can be easily connected to various existing bottle conveying lines. (3) Liquid level accuracy: The filling liquid level does not change with the bottle capacity, and the filling liquid level is consistent. (4) No dripping: The seal is tightly sealed, and if there is a broken or leaking bottle or no bottle, it will automatically not be filled or spilled. (5) Non breaking bottle: Using an elastic bottle support device, the bottle height error automatically adapts, with soft start, soft brake, no rigid impact, and no bottle breakage or damage to the machine. (6) # # Introducing foreign filling technology, using negative pressure equal position filling valve, good bottle guidance, accurate liquid level, fast filling speed, making the product superior to industry standards. 3. Characteristics of nitrogen flushing machine: (1) Adopting a rotating nitrogen flushing method, with a novel structure and working # #. (2) No bottle, no nitrogen filling to prevent nitrogen waste. (3) Adjust the nitrogen flushing height according to the bottle height, suitable for a wide range of bottle heights. (4) The bottle feeding process has elasticity and overload protection to prevent bottle breakage and damage to the machine. 4. Characteristics of the corkscrew machine (1) The structural design is novel, compact, and efficient. (2) Easy maintenance, few malfunctions, and long equipment lifespan. (3) Adjust the height of the stopper according to the height of the bottle, suitable for a wide range of bottle heights. (4) There is elasticity and overload protection during the bottle feeding and capping process to prevent bottle breakage and machine damage. (5) No bottle entry, no cork insertion to prevent cork waste. |
|||||||||||||||||||||||||||||||||||
Technical parameters:
|
|||||||||||||||||||||||||||||||||||
|